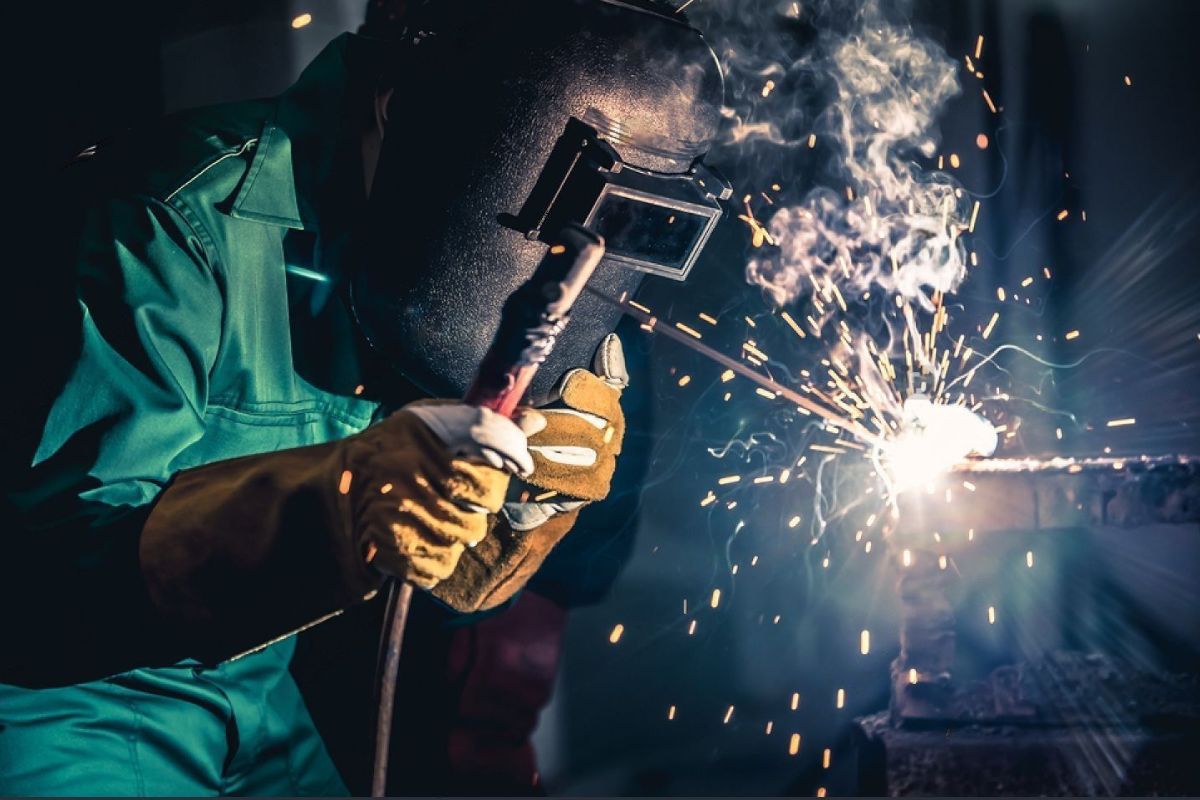
Enhancing Precision in TIG Welding: Why Remote Amperage Control Matters
Key Takeaways
- Understand the importance of remote amperage control in TIG welding.
- Explore the benefits of integrating advanced tools to improve welding precision.
- Receive practical tips for welders aiming to achieve superior results.
Table of Contents
- What Is TIG Welding?
- The Importance of Remote Amperage Control
- Benefits of Advanced Tools in Welding
- Practical Tips for Welders
- Data and Resources to Back Up the Information
- Final Thoughts
What Is TIG Welding?
TIG welding, or Tungsten Inert Gas welding, is a renowned technique for its precision and clean welds. Unlike other welding methods, TIG welding utilizes a non-consumable tungsten electrode to produce the weld. This method is highly favored among professionals due to the unparalleled control it offers over the weld area. It’s particularly effective for welding thin stainless steel, aluminum, and other non-ferrous metal sections.
The Importance of Remote Amperage Control
Remote amperage control enables welders to change the current while continuing the welding process, which is crucial for upholding the weld’s quality and consistency. This capability is particularly important for managing intricate welds that necessitate instant modifications. For example, using a Tig Torch Grip can significantly enhance the quality of your welds by enabling precise control over the amperage. Experts at Welding Pros emphasize that such constant adjustment leads to better penetration, reduced heat input, and superior weld quality. This control is particularly beneficial for heat-sensitive materials, preventing issues like warping and burn-through.
Benefits of Advanced Tools in Welding
Precision and Quality
Integrating advanced tools like remote amperage controls can significantly enhance welding efficiency. These tools provide finer control over heat input, critical for achieving consistent and high-quality welds. The ability to precisely manage the amperage ensures a uniform weld bead, reducing the likelihood of defects. This level of precision is not only essential for aesthetic purposes but also for the structural integrity of the weld, especially in critical applications like aerospace and medical devices. According to Welding Champs, this method is indispensable for projects requiring high accuracy and minimal contamination.
Ergonomics and Safety
Modern welding tools are designed with ergonomics in mind, aiming to reduce physical strain on the welder. Features like remote amperage control minimize the need for frequent repositioning, allowing for a more comfortable welding process. This reduction in physical strain is not just a matter of comfort; it directly impacts the welder’s efficiency and accuracy. Less physical stress means less fatigue, leading to fewer mistakes and a safer working environment. Safety is further enhanced by reducing the welder’s exposure to intense heat and harmful fumes for extended periods.
Cost-Efficiency
While advanced welding tools may require a significant initial investment, they can lead to substantial cost savings in the long run. Enhanced precision and control reduce the likelihood of errors, which means less material wastage and fewer instances of rework. Over time, these savings can offset the initial cost of the tools. Additionally, the improved efficiency can lead to faster project completion times, allowing for more projects to be undertaken within the same period, ultimately increasing …