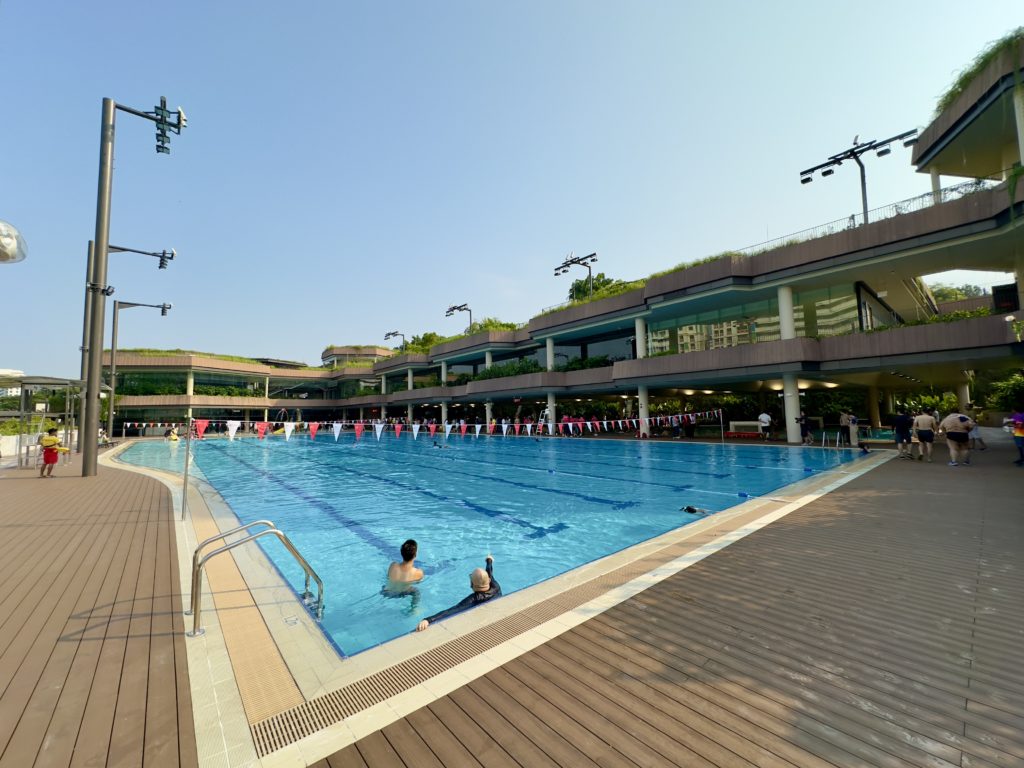
Bishan Swimming Coach: Elevating Water Confidence and Safety in Singapore
Located in the heart of Singapore, Bishan is a bustling estate where fitness, recreation, and education thrive. For those looking to master the art of swimming, Bishan Swimming Coach offers expert guidance to swimmers of all ages. Whether you are a beginner, an intermediate learner, or an advanced swimmer refining your skills, professional coaching ensures a safe and structured approach to swimming.
Coach Kelvin’s Perspective: The Importance of Learning from a Professional Coach
At a recent community event at Bishan Swimming Complex, Coach Kelvin, a seasoned and well-respected swimming instructor, shared his views on the importance of receiving proper swimming instruction.
“Many people think they can just pick up swimming by watching others, but there’s so much more to it than just staying afloat,” Kelvin explained. “Proper technique, breathing control, and water safety are crucial. Bishan Swimming Coach ensures that every swimmer not only learns how to swim but does so with confidence, efficiency, and the right safety knowledge.”
Kelvin emphasized that structured lessons under a qualified coach help swimmers avoid bad habits, reduce injury risk, and progress faster in their swimming journey.
Why Choose Bishan Swimming Coach?
With Singapore’s emphasis on water safety and recreational fitness, learning to swim has become a necessity rather than a luxury. Bishan Swimming Coach provides comprehensive training that caters to different swimming levels and goals.
Key Benefits of Bishan Swimming Coach:
- Personalized Training & Expert Guidance – Lessons are tailored to suit the learner’s experience level, whether they are just starting out or perfecting advanced techniques.
- Water Safety & Survival Skills – Learning essential water survival techniques such as floating, treading water, and rescue skills builds confidence and preparedness.
- Full-Body Fitness & Endurance – Swimming is an excellent low-impact exercise that enhances cardiovascular health, strengthens muscles, and improves flexibility.
- Confidence in the Water – Many people experience fear or discomfort in deep water. Professional coaching helps them overcome these challenges and build trust in their abilities.
- Social & Emotional Development – Learning in a structured environment fosters discipline, patience, and teamwork, all of which are valuable life skills beyond the pool.
A Thriving Swimming Community in Bishan
Bishan’s strong sense of community has made swimming lessons a popular choice for families, students, and working professionals. Unlike casual or self-taught swimming, Bishan Swimming Coach emphasizes proper technique, safety, and long-term water confidence.
Parents like Raymond Lee, whose son recently joined the program, shared his experience: “Before enrolling, my son was afraid of deep water. After just a few lessons, he’s more comfortable and excited about swimming. The structured approach at Bishan Swimming Coach has made a real difference!”
Start Your Swimming Journey with Bishan Swimming Coach Today
Whether you want to develop foundational swimming skills, refine your technique, or simply gain confidence in the water, Bishan Swimming Coach is here to help.
As Coach Kelvin always says, “Swimming isn’t just a skill; it’s a necessity. Start today, and the water will never be a challenge again.”
For more details on …